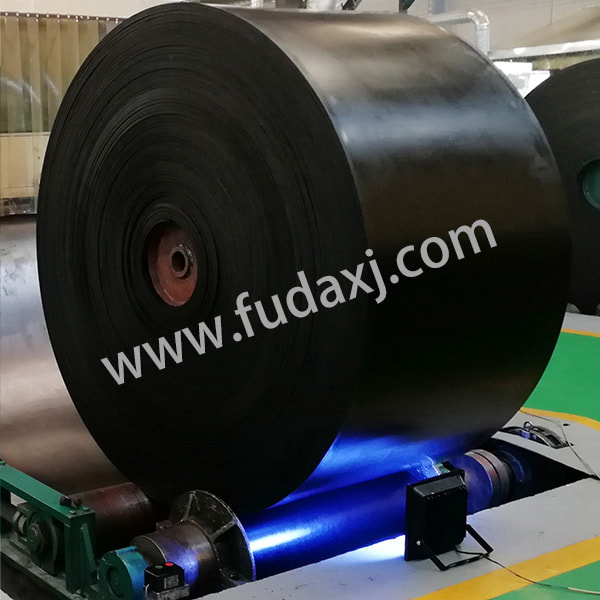
The transformation and upgrading of traditional Rubber conveyor belt production enterprises is not a matter of overnight. Many business leaders realize that transformation and upgrading will inevitably require a certain amount of investment in human, material, and financial resources. Small and micro rubber manufacturers have low profits and are exhausted to cope with fierce market competition. They have no more energy to transform and upgrade. More importantly, the heads of small and micro rubber production enterprises lack experience in factory transformation and upgrading, and the technicians around them cannot provide the company with a complete transformation and upgrading plan and goals, causing the transformation and upgrading of the factory to be "dead." From its own point of view, changing and upgrading the existing production model is risky. If the change is unsuccessful, it may "die", and if it is not changed, it will definitely be eliminated. This is the general trend of future enterprise development. Advanced capitalist countries have also experienced the pains of industrial transformation and upgrading, and the small, medium and micro enterprises that have survived have also undergone a rebirth and transformation.
The transformation and upgrading of traditional rubber manufacturing enterprises is a complex system engineering, which involves raw material procurement management, production process reengineering, equipment and process improvement, production process and automation system integration, product formulation research and development and product quality improvement, production site management and on-site Industrial engineering analysis, re-planning of warehousing and logistics systems, customer relationship management and many other aspects. The above changes really require a person or team with multiple technical knowledge and industry experience to achieve work. Due to certain confidentiality factors, it is impossible to provide you rubber friends with real-life pictures and key information in various aspects of advanced foreign rubber factories. Fully automatic production equipment or assembly lines, which are only reflected in the broad cognition of everyone, are very advanced in every aspect of factory operation.
For the transformation and upgrading of traditional rubber manufacturing enterprises, I think we must first develop a complete set of effective upgrade plans based on the company's own situation, because each company's own situation is completely different. You can't copy or make changes in a model, but you must find a path of transformation that suits you. Then the plans are decomposed layer by layer and the transformation and upgrading goals are set one by one, and finally implemented in stages. At the beginning of the improvement, I think the following aspects need to be done first:
First, in accordance with national industrial policies and environmental protection requirements, continuously improve its own enterprise construction, actively respond to national guidance policies and major environmental protection requirements, and take the initiative to rectify the original environmental pollution problems.
Increase or upgrade environmental treatment equipment, and vigorously improve the on-site production environment of the workshop. In particular, pollution control is carried out for key polluted processes or workstations on the production site. For example, in a rubber mixing production workshop without an internal mixing system, the dust and waste gas generated when powder materials such as carbon black are added. Increase the power, air volume and processing capacity of the original waste gas collection and treatment equipment. The production workshop (rubber mixing, vulcanization molding), post-processing engineering, online quality inspection and packaging workshop, raw material warehouse, finished product warehouse, carbon black drug measurement area, and quality inspection room are reasonably arranged and distinguished according to the production process.
Second, the production equipment should be assembled into an assembly line as far as possible in accordance with the product production process, and the complex processes are decomposed one by one.
The simple procedures that were previously completed manually should be completed with equipment as much as possible. For example, for simple material transportation, a complete material transportation system is established between the main production equipment. The demand and delivery of the original and auxiliary materials of the workstation, and the samples for online quality inspection are also done with material conveying equipment as much as possible. The principle is to set up a high-efficiency production line, so that all equipment and production personnel conform to the production process of the product, so that the production cycle is more regular and smooth. If the production line has been set up before, then find the bottleneck station for targeted improvement. Build a complete product quality management system. Try to reduce the product's bad processes caused by human factor interference. Let stable equipment and a variety of sensors replace human factors. For example, for the management of cooling water, in the past, we might delineate a management scope by ourselves and ask workers to record the thermometer on the cooling water pipe every day, but this did not form a closed-loop management, and we should focus on management for extremely temperature-sensitive workstations.
Third, comprehensively improve the ability of product quality inspection, strengthen on-site production quality control, and minimize fluctuations in the uniformity of rubber product production quality.
Our company is not unable to produce high-quality products, but what we lack is always producing high-quality products. This is the gap between our small and medium rubber companies and excellent companies.
Fourth, reengineering the factory operation process, using a more scientific method to change the original factory operation process.
This not only refers to the production process, but also includes the factory material system process, production management process, financial management process, and so on. To put it bluntly is to change the original backward management concept and make the factory operation process more scientific and efficient.