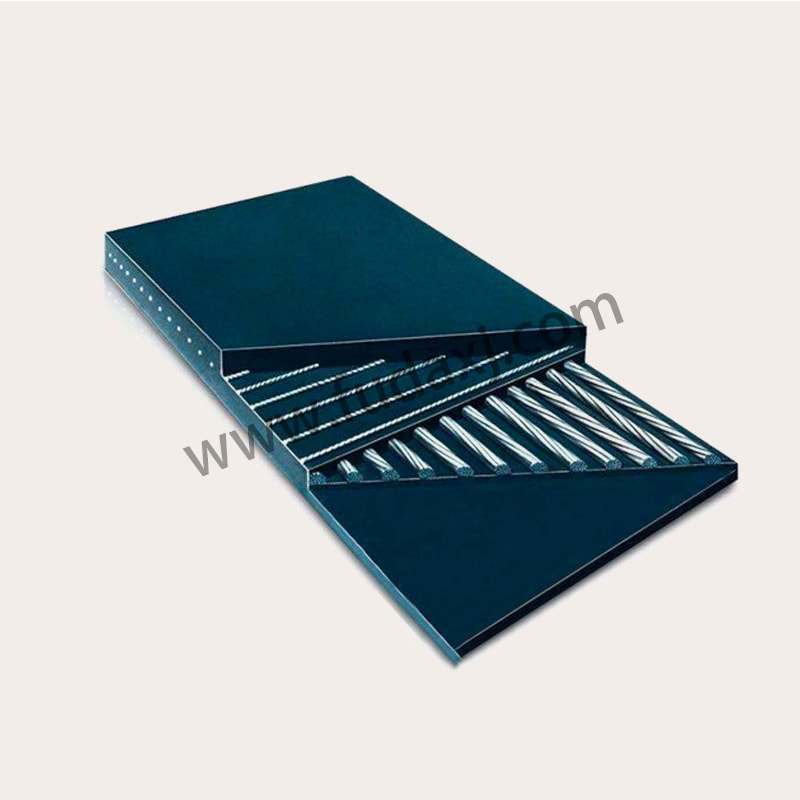
1. Improve the conveyor belt drop hopper. Improving the conveyor belt drop hopper is one of the effective measures to prevent the early damage of the conveyor belt. Improve the drop hopper at the transfer point of each belt conveyor to increase the ability to pass foreign objects by 2.5 times. Long and large foreign objects are not easy to get stuck between the funnel wall and the conveyor belt during the conveying process, and the foreign objects tear the conveyor belt. Probability.
The guide apron at the blanking hopper makes the gap between the conveyor belt and the conveyor belt larger and larger along the running direction of the conveyor belt, which solves the problem of coal and stones jamming between the conveyor belt and the apron, and eliminates the conveyor belt caused by this. damage. The hopper with a large drop has a buffer baffle installed inside to prevent the material from directly impacting the conveyor belt.
2. Add a scraping device at the reversing roller. A scraping device is installed at the reversing drum along the conveyor belt to eliminate the problem of material adhesion at the reversing drum and solve the local damage of the conveyor belt caused by the sticking of the drum.
3. The improvement of the conveyor head, tail and intermediate transfer transition. The transition length and transition mode at the head, tail and intermediate transfer of the conveyor have a great impact on the service life of the conveyor belt. Reasonable transition design must be carried out, and the wear of the rubber surface of the conveyor belt should be reduced as much as possible to ensure that there is no folding or bulging of the conveyor belt, and no material leakage at the blanking place.
4. The pressure roller of the conveyor at the concave transition. Practice has proved that the lateral strength of the steel rope conveyor belt is insufficient. When starting, the pressure roller causes the conveyor belt to be partially stressed, which causes the conveyor belt to be torn. Changing the pressure roller to the belt roller can completely solve this problem. .
5. The counterweight of the conveyor belt of the large machine arm support is reduced. The initial service life of the conveyor belt of the stacker arm frame of the coal mine system is very short. The overweight design of the counterweight is an important reason for the excessive tension of the conveyor belt and the premature cracking and aging. On the basis of meeting the material tension of the conveyor belt and reducing the counterweight, the service life of conveying coal will be extended from 1.5 million tons to 4.5 million tons. The original designed counterweight of the 200,000t mining system stacker-reclaimer arm conveyor belt is 25t (including the weight of the counterweight drum). After a load shedding to reduce the counterweight by 6t, the domestic ordinary steel wire belt was used, and the work volume exceeded 8 million tons.
6. Material flow direction adjustment. The direction of material flow has an important influence on the service life of the conveyor belt. The material flow should run in the same direction as the conveyor belt, which can greatly increase the service life of the equipment.