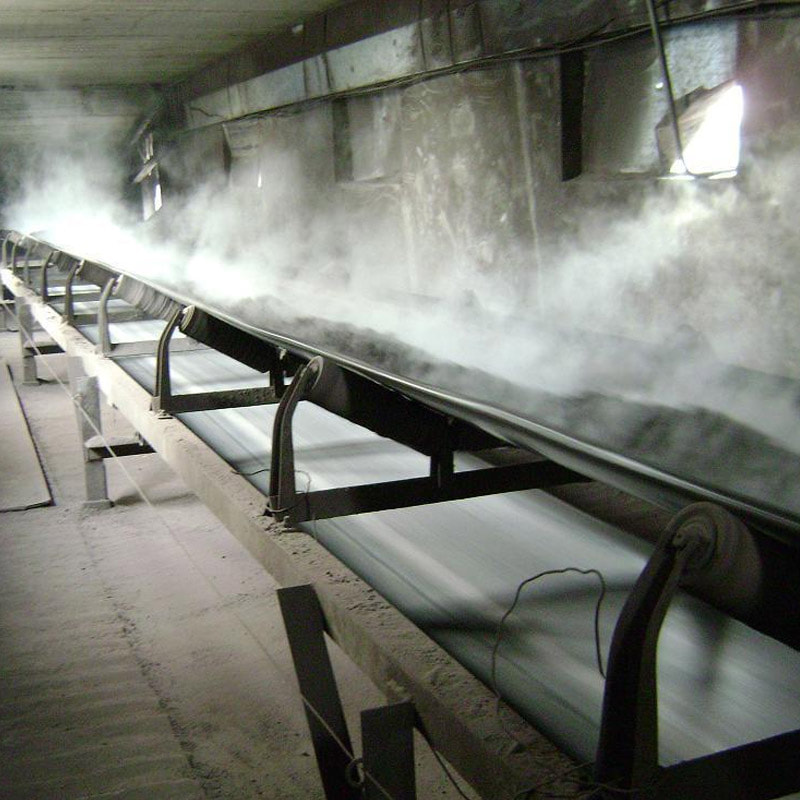
Various studies have been carried out to determine the effects of steel cord diameter, rubber thickness and number of steel cords on the strength of conveyor belts. In this study, Abaqus/CAE was used to establish the finite element models of conveyor belts. Compared with the experiment, the simulation results are in good agreement.
Rubber thickness increase increases the pullout force of a conveyor belt. However, the rate of increase is slow. The pullout force increases more than the steel cord diameter increase. It is a linear relationship.
The pullout force is also increased when there are more steel cords on a side. This does not mean that the tension is increased.
In the experiment, the pullout force of four steel cords was higher than that of one steel cord. This was because the two steel cords on one side were not as strong as the two steel cords on the other side.
The tensile experiments were also carried out to verify the simulation results. The simulation results and the tensile experiment were both in good agreement.
Steel cords are first cut with a special tool. Then, they are gently buffed with a grooved rotary wire brush. They are then slightly coated with a special rubber solution. They are then placed on a separation cloth. Then, an unvulcanized cover rubber sheet is placed on top of the separation cloth. The cover rubber can be filled with fiber or ST.
Next, a wedge-shaped strip is cut out of the upper cover to expose the steel cords. The edges of the steel cords are tapped thoroughly. The rubber solution is then applied to the splice area.